
PLASTIC MOLDING at ASH comes in all sizes
Anything from small medical parts to large hollow kayaks, we can mold it. Injection molding for parts up to the size of a microwave oven and rotational molding for parts up to 16 feet.
And we are specialists in highly engineered resins like nylons, PEEK and more. Call us to find out more.

SEE the MINDS and MACHINES


ASH INDUSTRIES is an engineering centric American plastic injection molding company with in-house mold building and tool room.
How we truly gain a client's trust is that we welcome the challenges, the projects that need thinking and trying different things. We are engineers who THINK with you. In fact very few other injection molders share the same passion for making great products as we do.
ASH has been thermoplastic injection molder for over 30 years and our list of projects is vast, spanning a wide gamut of industries and OEM projects. Need a medical or surgical device? How about an overmolded structural component? Maybe you want better grip for a firearm? It's what we do.
Certs? no problem, we understand FDA, FAA and FFL requirements so you know that you are working with experienced injection molders and we have a class 7 clean room.
We experiment with you, we offer new materials, we have engineers on staff to offer alternative solutions. We are on your team to make your parts better.
.png)

How does ASH injection mold your parts?
Engineered plastic pellets are fed into a heated barrel with a rotating screw that melts the plastic and mixes it evenly. The molten plastic is then injected into a closed mold with high pressure. The plastic cools and hardens within the mold to its final shape, and then is ejected from the mold.
Injection molding can produce large quantities of identical parts quickly and efficiently. And they can have complex geometry with undercuts and hollow interiors with very tight tolerances.
Production cost per part decreases with higher quantities so long runs are great.
-
High tolerance with repeatability
-
Cost goes down with higher quantities
-
Materials available have amazing properties
-
Complex geometries
SCROLL through the shop

HIGHLY ENGINEERED
RESINS
Thermoplastic injection molding can be accomplished with just about any plastic resin like ABS, nylon, PET, polypropylene, polyethylene and TPE. At ASH, we like to mold the tough stuff. Engineering-grade resinssuch as lexan, PEEK, noryl, valox and ultem.
The variety of resins allows product developers to experiment with different materials and surface finishes for their products. And with our SUPERMOLD program you can get prototype runs made in the actual material for field tests, which is much better than 3D printing samples.


DESIGNING FOR MANUFACTURING
Designing for Manufacturing (DFM) in plastic injection molding optimizes efficiency by minimizing material waste and simplifying part geometries which can lower tooling costs and ensure product quality.
Collaboration between design engineers and manufacturing experts addresses material selection and regulatory compliance, guaranteeing successful outcomes in plastic injection molding.
MOLD
BUILDING
Our skilled toolmakers use computer-aided design (CAD) to develop the mold's intricate details, including parting lines, gating, and cooling channels.
The quality and precision of the mold directly impact the final product's consistency, efficiency, and overall manufacturing success.
See below to learn more about the mold building process...
MATERIAL SELECTION
We work closely with you to select your part's material based on the specific requirements of the project.
Considerations include: Mechanical Properties, Thermal Properties, Chemical resistance, Functionality, Appearance, Regulatory Compliance & more...
Prototyping and testing are then conducted to validate material choices and ensure that the final product meets performance expectations.
INSERT + OVERMOLDING
Insert molding and overmolding are specialized plastic injection molding techniques that involve molding additional components or materials onto or around an existing substrate.
Common applications of insert molding include adding metal inserts for increased strength or incorporating electronic components, such as connectors or sensors, directly into a plastic part.
THE ADVANTAGES OF PLASTIC INJECTION MOLDING
PRISTINE SURFACE FINISHES
Executed with a variety of general and engineering-grade resins with pristine surface finishes
PREDICTOR OF MANUFACTURABILITY
Thermoplastic injection molding can be utilized for prototyping purposes.
SPEED
Parts that are thermoplastic injection molded are typically turned around within days.
Injection molding allows for high precision and consistency in producing complex and detailed parts.
PRECISION

If you Google "BEST injection molding company near me..."
Try looking a bit further. Location does not matter, in fact down here at ASH, our work ethic and neighborly way of life means better products for you. We can ship anywhere and you cant beat our customer service.



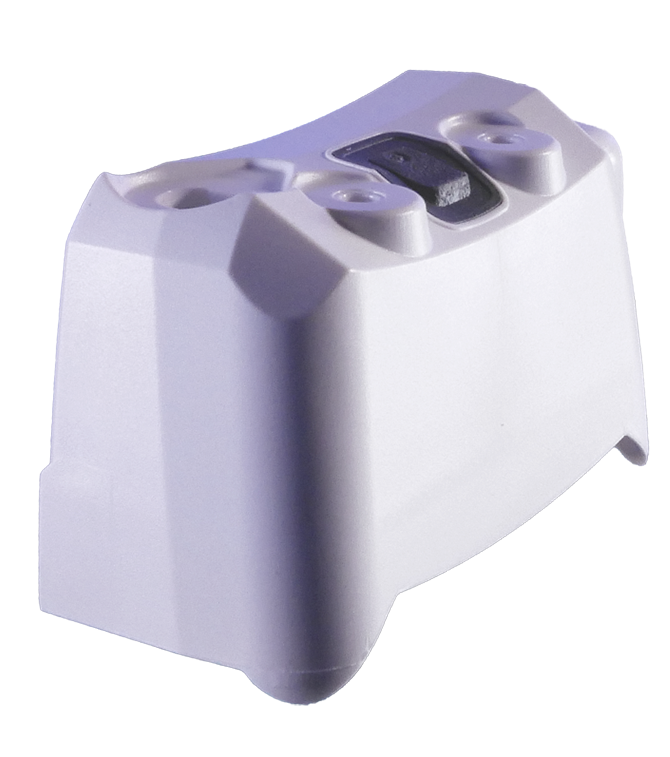
WE THINK
WE SOLVE
WE MOLD.
PRECISION
Thermoplastic injection molded parts are able to be produced with pin-point accuracy, which is a major advantage over other prototyping processes like 3D printing.
FANTASTIC SURFACE FINISH
Thermoplastic injection molding can be executed with a variety of general and engineering-grade resins. The process is also able to create parts with pristine surface finishes, which makes the production process viable to create not only prototypes, but small and large production runs. Rough or pebble textured surface finishes can also be created with the production process.
SPEED
Parts that are thermoplastic injection molded are typically turned around within days. If it's used for prototyping, this allows developers to make design changes quickly, thereby enabling it to go to market sooner. The longest part of the injection molding process is the time that needs to be spent creating the mold. However, molds can also be created to fine-tune prototypes and then used again for a manufacturing run.
PREDICTABLE MANUFACTURING
Thermoplastic injection molding can be utilized for prototyping purposes. And here's why - parts can not only be completed and turned around quickly with days, but the two benefits of the technology mentioned above, accuracy and surface finish quality, make the process a great predictor of manufacturability.
Often times, developers will order several early prototyping runs on other technology, then use thermoplastic injection molding to validate product design prior to green-lighting the product for manufacturing. Since parts can be crafted in several different resins, developers will also experiment with surface finishes and materials to see what they want to manufacture in.
IF YOU NEED SHORT RUN PARTS, FAST THEN TRY OUR SUPERMOLD PROGRAM

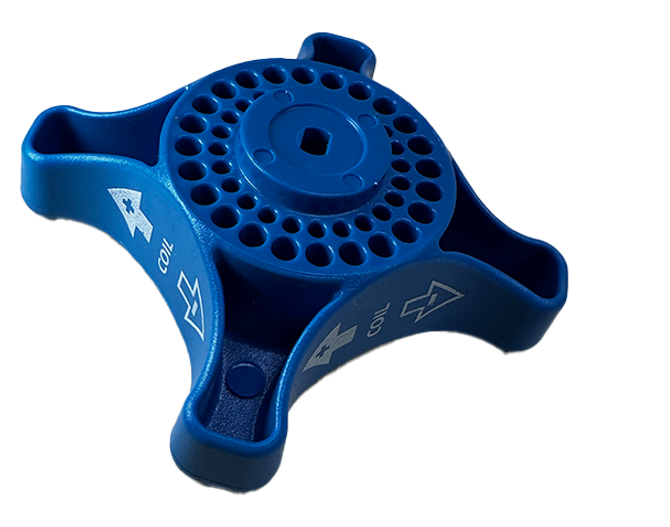
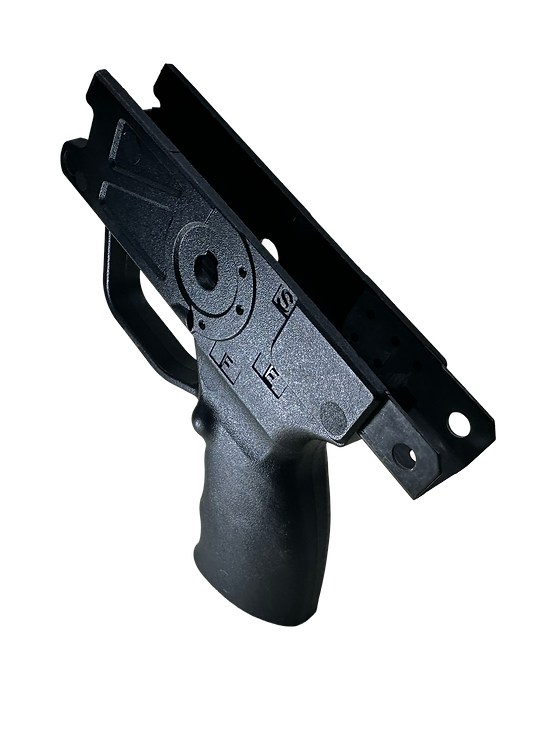


HOW DO YOU GET YOUR PARTS MADE QUICKLY?
STEP 3. SELECTING YOUR MATERIAL
We work closely with you to select your part's material based on the specific requirements of the project.
Considerations include: Mechanical Properties, Thermal Properties, Chemical resistance, Functionality, Appearance, Regulatory Compliance & more... Common injection molding materials include ABS, nylon, polypropylene, and polycarbonate. At ASH we also go beyond the ordinary and can work with very exotic materials.
Prototyping and testing are then conducted to validate material choices and ensure that the final product meets performance expectations.
STEP 2. BUILDING YOUR MOLD
Designing the mold is often considered one of the most laborious and expensive steps of plastic injection molding process. The complexity of designing a mold stems from the need for precision, consideration of material properties, and the tonnage capabilities of the presses.
If you have a mold built by an outside mold shop you have to rely on the new supplier to be able to check it and integrate it into their presses. This is why an in house toolroom is critical.
Mold design often involves an iterative process of testing and refining. Prototypes may be created, and adjustments to the mold design are made based on the feedback from these prototypes.
5. VALUE ADDED SERVICES: INSERT MOLDING & OVERMOLDING, ASSEMBLIES and PACKAGING
Insert molding and overmolding are specialized plastic injection molding techniques that involve molding additional components or materials onto or around an existing substrate.
Common applications of insert molding include adding metal inserts for increased strength or incorporating electronic components, such as connectors or sensors, directly into a plastic part.
We actually did a project where overmolding a metal support increased its strength by a factor of two while keeping it corrosion free in use.

STEP 1. DESIGN FOR MANUFACTURING CONSULT
This is a critical step as it determines the mold configuration and overall cost and efficiency. Design for Manufacturing (DFM) in plastic injection molding starts with a collaboration between you and our engineers to address part design, draft angles, prototyping, environmental needs, lifecycle expectations, regulatory compliance, and more to ensure a successful outcome.
We don't just quote and mold, we help you think. You deserve the value added services that will make your part or component excel in the field.
Here's why our design-to-manufacturing approach is a game-changer:
-
Optimizes efficiency
-
Minimizes material waste
-
Simplifies part geometries
-
Lowers tooling costs
-
Ensures product quality
4. CLAMP, INJECT, COOL
Quality and workflow is dependent on the press size.
The injection molding machine's clamping force or tonnage, is set based on the specific part and material being processed. Insufficient tonnage can lead to flash (excess plastic) formation or mold parting, while excessive force can damage the mold or shorten its lifespan.
How the part cools also affects the material properties, some parts need coolant in the mold, we have the ability and experience to determine the right methods.


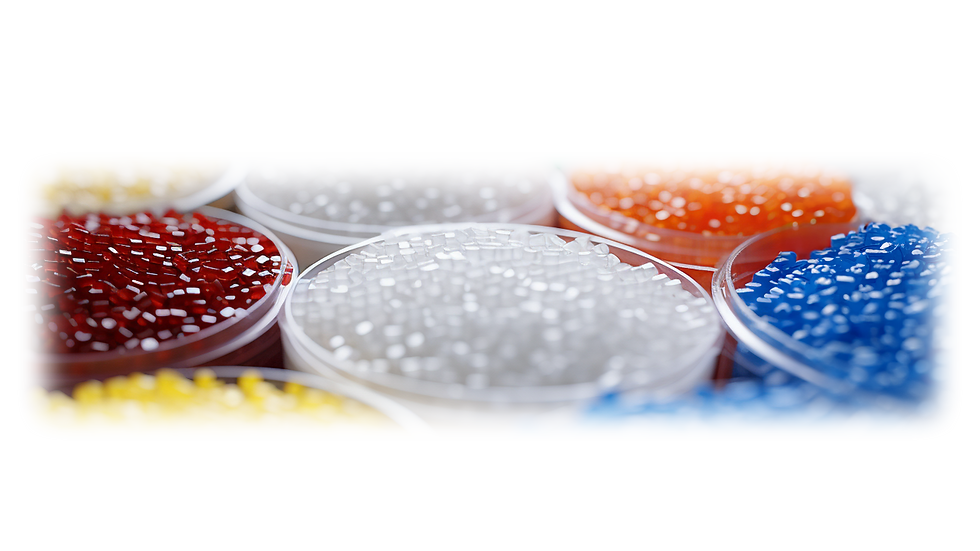

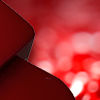
Drop us a note and we'll get back and gladly help you conquer your molding challenges.
What else can we help you with?

ASH Industries, Inc.
Molding experts in Lafayette, LA
1330 W Willow St.
Lafayette, LA 70506
CONTACT:
Becky Herpin
(337) 235-0977